1 What Is Quality Inspection?
Objectives of a quality inspection process
Core elements of an inspection checklist
4 Why Is Quality Inspection Important?
5 Types of Quality Inspection
Incoming Inspection
In-Process Inspection
Final Inspection
Specialized Inspections
10 Importance of Quality Inspection in Manufacturing
11 How Does Quality Inspection Connect QMS and PLM
12 Why Quality and Safety Leaders Need to Automate Inspection Management
Challenges of manual inspection
Advantages of Automated Inspection Management
15 How Qualityze Simplifies and Strengthens Quality Inspections for Modern Businesses
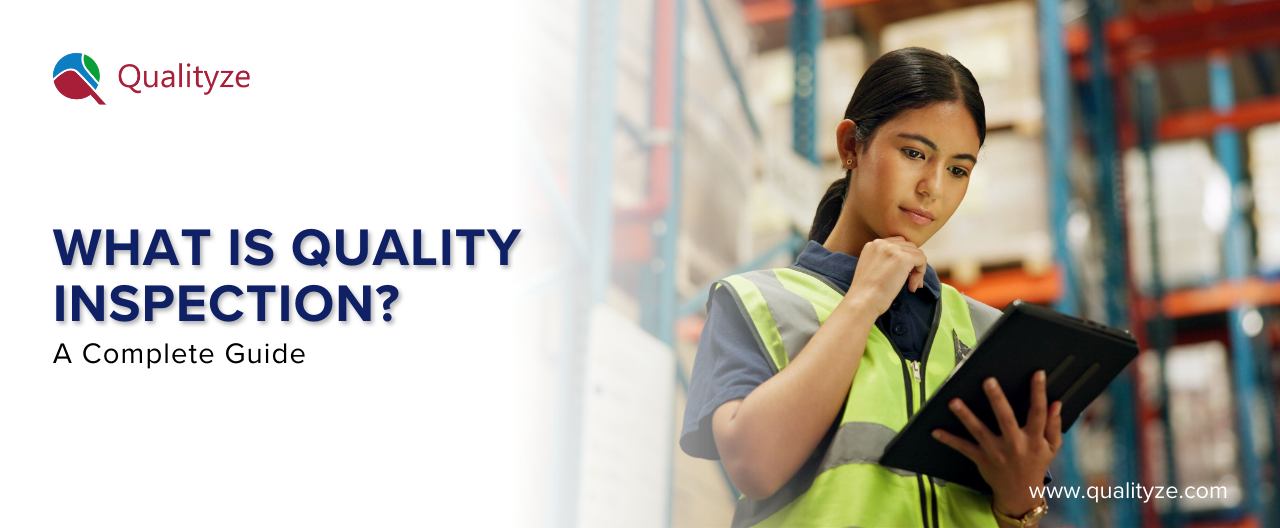
Quality inspection sits at the heart of any robust manufacturing or service operation. By systematically examining products, components, or processes against defined standards, quality inspection ensures that every deliverable meets customer expectations, regulatory requirements, and internal benchmarks. As W. Edwards Deming famously said, “Quality should be built in, not inspected in.” This guide will walk you through everything you need to know—definitions, importance, types, integration with QMS and PLM, the case for automation, and how Qualityze can transform your inspection program.
What Is Quality Inspection?
Definition of quality inspection
Quality inspection is the process of measuring, examining, and testing products, parts, or processes against specific requirements or standards. Unlike quality assurance (a preventive set of activities) or quality control (the broader framework that includes inspection, testing, and corrective actions), inspection focuses on hands-on verification activities—visual checks, dimensional measurements, functional tests, and more.
Objectives of a quality inspection process
- Defect detection: Catch nonconformities before they reach customers.
- Process validation: Confirm that production steps yield parts within tolerance.
- Compliance verification: Ensure adherence to industry regulations (e.g., ISO 9001, FDA 21 CFR Part 11).
Core elements of an inspection checklist
- Visual inspection items: Surface finish, color, markings.
- Dimensional checks: Caliper readings, gauge verifications.
- Functional tests: Electrical continuity, pressure holds, leakage tests.
A well-structured inspection checklist drives consistency, minimizes human error, and forms the backbone of any inspection management system.
Why Is Quality Inspection Important?
Reducing defects and costs
Poor quality hits the bottom line hard. According to the American Society for Quality (ASQ), the Cost of Poor Quality (COPQ) can range from 10% to 20% of a company’s annual revenue—that’s up to $20 million wasted each year on a $100 million business.
Protecting brand reputation and compliance
A single recall can erode customer trust overnight. Over 65% of manufacturers still rely on manual inspection methods—and 40% of these face frequent product recalls as a result. Robust inspection processes don’t just catch defects; they safeguard your reputation and ensure regulatory compliance.
“Quality is everyone’s responsibility.”
— W. Edwards Deming
Driving continuous improvement
Inspection data feeds root-cause analyses, enabling teams to tackle systemic issues rather than band-aid fixes. Over time, this data-driven approach reduces scrap, rework, and warranty claims—turning inspection from a cost center into a competitive advantage.
Types of Quality Inspection
Understanding the types of quality inspection helps you deploy the right checks at the right time:
Incoming Inspection
Incoming Inspection, or Incoming Quality Control (IQC), verifies that supplier provided raw materials, components, parts meet predefined specifications before they enter the production process. Technicians inspect material certificates, measure critical dimensions with calipers or micrometers, and perform material tests—such as hardness checks on metal billets or moisture analysis in plastic resins. For example, an aerospace manufacturer might use a handheld spectrometer to confirm the alloy composition of aluminum extrusions upon delivery. By catching deviations at the dock door, IQC prevents substandard inputs from cascading into costly production disruptions.
In-Process Inspection
In-Process Inspection takes place at key stages within the manufacturing workflow, either continuously on-line or periodically off-line. On-line inspection integrates sensors and gauges directly into equipment—such as laser micrometers measuring pipe diameters in real time—while off-line inspection uses statistical sampling plans to examine selected batches in a quality lab. In a pharmaceutical tablet line, for instance, in-process checks include weight variation sampling and tablet hardness tests at every production shift. This balanced approach ensures critical parameters remain within control limits without inspecting every single unit.
Final Inspection
Final Inspection serves as the last quality gate before products ship to customers. Inspectors conduct comprehensive audits against release criteria—visual appearance, functional performance, and packaging integrity. In the electronics industry, final inspection may include operating each device through power-up routines, verifying firmware versions, and confirming label accuracy. A medical device manufacturer, for instance, will perform leak tests on assembled infusion pumps and validate alarm functionality. Final Inspection safeguards brand reputation by ensuring only compliant, fully tested products reach the market.
Specialized Inspections
Specialized Inspections employ advanced testing and automation techniques tailored to specific applications:
- Non-Destructive Testing (NDT): Methods such as ultrasonic flaw detection in welded joints, radiographic X-ray imaging of castings, and magnetic particle inspection of steel forgings detect internal defects without harming the part.
- Automated Visual Inspection: High-speed machine-vision cameras scan surfaces for scratches, dents, and missing features—commonly used in automotive paint shops to flag paint runs or chips on body panels.
- Digital Inspection Tools: Coordinate Measuring Machines (CMMs) and 3D laser scanners generate precise digital replicas of complex geometry—ideal for verifying tight tolerances on aerospace turbine blades or injection-molded plastic housings.
By orchestrating Incoming, In-Process, Final, and Specialized Inspections into a unified strategy, organizations secure end-to-end quality coverage—detecting issues at their origin and preventing defects from reaching downstream stages.
Importance of Quality Inspection in Manufacturing
Manufacturing environments are complex ecosystems where a single defect can ripple across the supply chain. Here’s why quality inspection in manufacturing is non-negotiable:
Integral to Quality Control (QC)
- Real-time defect tracking: Automated inspections feed data into dashboards, highlighting defect trends and hotspots.
- Root-cause analysis integration: Inspection failures seamlessly link to CAPA workflows, accelerating corrective actions.
Regulatory and Industry Standards
- ISO 9001:2015 mandates a process-based approach, where inspection data proves process capability and product conformity.
- ANSI/ASQ Z1.4 (ISO 2859-1) defines statistical sampling plans to balance inspection effort with risk.
- FDA 21 CFR Part 11 requires secure, audit-ready records for electronic data—a must for pharmaceutical and medical device sectors.
Operational and Financial Impact
- Reduced scrap and rework: Early detection avoids cascading rework downstream.
- Minimized warranty claims: Products leaving the factory meet specifications.
- Lower total cost of quality: Investing in inspection prevents far more expensive failure costs.
By embedding inspection into manufacturing workflows—rather than treating it as a post-mortem check—organizations gain visibility, traceability, and control over product quality.
How Does Quality Inspection Connect QMS and PLM
Linking Quality Management System (QMS) with Product Lifecycle Management (PLM) unlocks transformative insights:
- QMS as the data hub
-
- All inspection results feed into a centralized QMS database, creating a single source of truth for quality metrics.
- PLM drives design improvements
-
- Inspection feedback loops into PLM, informing engineering teams of real-world performance issues and enabling design-for-quality.
- End-to-end traceability
-
- From initial product design (PLM) → manufacturing inspections (QMS) → corrective actions (CAPA) → documented records (Audit).
-
- This traceability ensures any nonconformance can be traced back to the design specification or process step that needs adjustment.
Integration benefit:
When inspection data flows bidirectionally between QMS and PLM, companies achieve faster design-for-manufacturability cycles, fewer product iterations, and more confident regulatory submissions.
Key search terms to weave in: QMS PLM integration, product lifecycle quality, inspection feedback loop.
Why Quality and Safety Leaders Need to Automate Inspection Management
Manual inspection workflows—paper checklists, spreadsheets, slow data entry—are a recipe for errors and delays. Here’s why inspection management software is now table stakes:
Challenges of manual inspection
- Human error: Illegible handwriting, transcription mistakes.
- Delayed reporting: Bottlenecks in gathering, aggregating, and analyzing data.
- Audit risk: Difficulty proving compliance with timely, accurate records.
Advantages of Automated Inspection Management
- Mobile data capture: Inspectors use tablets or handheld scanners to record results on the shop floor.
- Real-time alerts and notifications: Failed inspections auto-trigger CAPA tasks, ensuring rapid containment.
- Audit-ready digital records: Secure, timestamped logs meet ISO and FDA criteria without manual filing.
- Advanced analytics and KPIs: Visual dashboards track inspection pass rates, defect density, and inspector performance.
For quality and safety leaders, automation means shifting from reactive firefighting to proactive risk management—spotting patterns before failures escalate.
How Qualityze Simplifies and Strengthens Quality Inspections for Modern Businesses
Qualityze Inspection Management delivers an end-to-end, cloud-native solution that embeds best practices into every inspection. Here’s how it helps you win at quality:
Key Features
- Configurable inspection plans: Build checklists, sampling schemes, and acceptance criteria with drag-and-drop ease.
- Mobile-ready inspections: Perform checks offline on tablets or smartphones; sync automatically when back online.
- Statistical sampling modules: Choose ANSI/ASQ Z1.4 sampling plans or define custom rules.
- Machine-vision integrations: Connect to automated visual systems for high-speed optical inspections.
AI-Driven Insights
Qualityze AI engine analyzes historical inspection data to:
- Detect emerging defect patterns before they become critical.
- Recommend optimal sampling frequencies based on defect trends and risk profiles.
Seamless EQMS Integration
Inspection findings automatically link to other Qualityze modules:
- CAPA: One click to launch corrective action—with root-cause investigation tools built-in.
- Audits: Inspection records populate audit evidence, reducing preparation time by up to 50%.
- Supplier Quality: Push incoming inspection results directly into supplier performance dashboards.
Would you like to experience Qualityze difference to transform the inspection processes?
If manual inspections are slowing you down, or if you’re chasing data across spreadsheets and file cabinets, it’s time for a change. Qualityze Inspection Management empowers quality and safety leaders to automate, analyze, and act—transforming inspection from a burdensome chore into a strategic advantage.
Request a demo today and discover how Qualityze can simplify your inspection workflows, strengthen compliance, and drive continuous improvement—so you can deliver excellence, every time.
Share
The Start of Something Amazing.
Request Demo
Products
Industries